Waterjet Cutting Process
Whether you are cutting rubber, metal, plastic, ceramic, or composites, we can help you. Abrasive Waterjet of Indiana’s cutting process promises smoother finishes, faster turnaround, and higher quality of products. You and your company can definitely
gain significant savings in time and money.
Our State-of-the-Art Cutting Services
Being 5–10 times faster than wire EDM machining and having no significant induced heat, waterjet cutting stands above other typically used methods. It is also better than lasers when it comes to cutting reflective mediums. Tolerances are within ±.005 and
five edge qualities (Q1 to Q5) are attained in most materials.
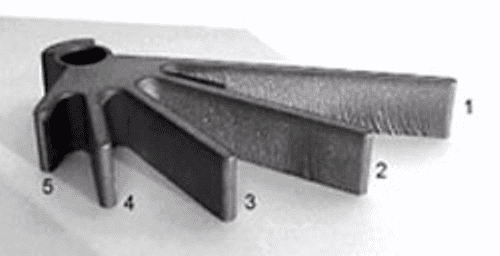
Quality Finish
Materials cut by the abrasive waterjet machines have smooth, satin-like finish—similar to a fine sandblasted finish. Our process can also achieve five edge qualities:
- Edge Quality 1 (Q1) – Separation Cut
- Edge Quality 2 (Q2) – Medium Rough Cut
- Edge Quality 3 (Q3) – Standard Machining Cut
- Edge Quality 4 (Q4) – High-Quality Finish
- Edge Quality 5 (Q5) – Very High-Quality Finish
No Heat in Machining Process
Abrasive waterjets can cut materials at room temperatures. This means that there are no heat-affected areas or structural changes in materials when using this process. These machines can also harden metals and other composites with low melting points.
Environmentally Friendly
These waterjet machines use garnet as an abrasive. Garnet is a reddish natural crystal with a 6.5–7.5 Mohs hardness. No noxious gases or liquids are used in abrasive waterjet machining, nor are there any oils used in the process.
There’s no need to change tools! A wide range of conventional processes can be performed with this single tool. These include:
- Drilling
- Sawing
- Gear Cutting
- Punching
- Slitting
- Spline Cutting
- Blanking
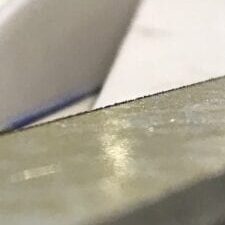
Minimal Burr
No heavy burrs are produced by the abrasive waterjet process. Parts can often be used directly without deburring.
Why Choose Us
When tight tolerances and fast turnaround are the concern, Abrasive Waterjet of Indiana’s precise waterjet cutting services can help meet your needs. Most of our cost- and quality-conscious customers choose us over other shops as we consistently achieve close tolerances and intricate features. Compared to the conventional CNC machining, our services can cut up to 40–60% of the time—saving labor hours for more complex processes.
We also run the latest technologies in the waterjet industry. As one of the largest waterjet companies in the state, we have 4 machines: OMAX 2652, 55100, and 2-80x waterjets. We offer taper free cutting for optimal precision. One of our machines has multiple cutting heads for production volumes. We even have the rotary axis that adds another level of cutting to our process.